FROM THE CTO
‘Petrogas was established in 1949 and initially worked mainly for the Dutch urban gas industry. We were also an early adopter of LPG automotive gas, building the first LPG filling station in the Netherlands. Towards the end of the 1950s, after the discovery of the gas fields at Slochterveld, we shifted our attention to natural gas.
Innovation and market expansion are core elements of our operational management. Over the course of the years, Petrogas has developed a stronger focus on energy production, in which sustainability plays an important role. By anticipating our customers’ needs and treating them as we would want to be treated ourselves, Petrogas has enjoyed significant growth. I would like to thank our people, our customers and our suppliers for believing in us and supporting us.’ Chris van der Ree, CTO
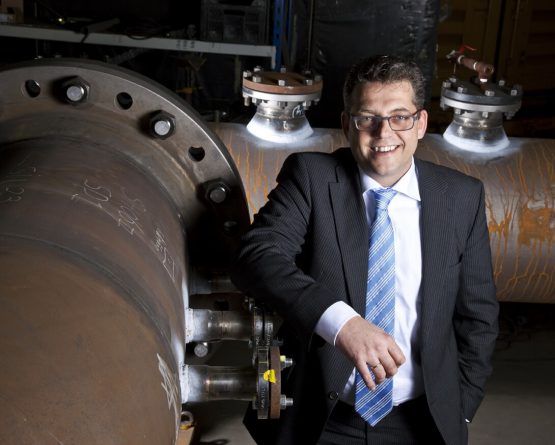
OUR VISION
We have the world on loan from the generations that will follow us and must care for it in good stewardship. Ultimately, responsible global energy production will become completely based on renewable sources of energy.
Petrogas has a key role in that future vision and is continually applying its expertise in new, innovative ways. In the decades it will take to transition to a renewable energy system, we will provide the technology that makes it possible to use the planet’s reserves and natural resources with maximum efficiency.
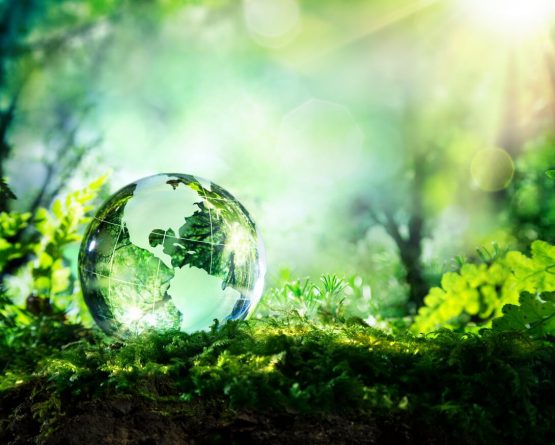
OUR MISSION
To create and deliver high-quality, effective processing systems that enable our customers to maximise their use of the available natural resources, with minimal environmental impact.
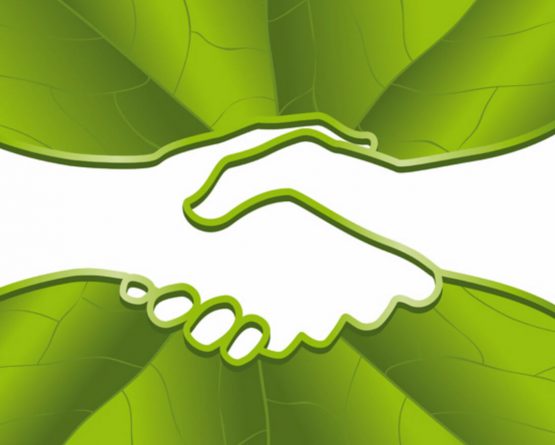
HOW WE WORK
The heart and brains of Petrogas are a team of committed process specialists.
Using our extensive experience and driven by our passion for technology, we design and deliver tailor-made processing systems that provide maximum value for our customers in the gas and energy industries. We consider our customers’ challenges as our own and we don’t step out until everything works as it should. Our service and support guarantee smooth and effective functioning during the entire lifetime of our systems. Our clients value our reliability and say that we are great to work with. That’s because we treat the people we engage with as we would want to be treated ourselves. To do what we do, we must stay at the forefront of technology. Petrogas invests heavily in R&D, with the long-term focus of our innovation squarely on renewable energy production.
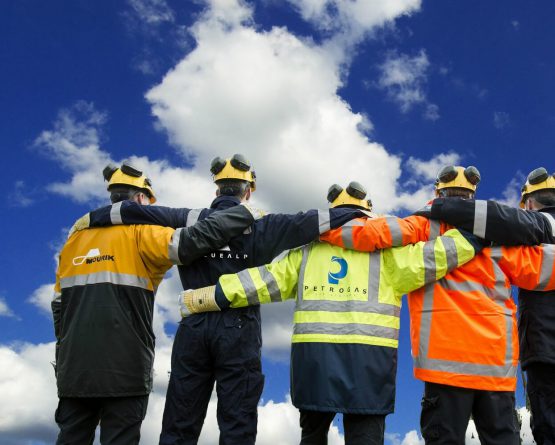
BEGINNING
Petrogas was established in 1949 and initially worked mainly for the Dutch urban gas industry.
We were an early adopter of LPG automotive gas, building the first LPG filling station in the Netherlands. Towards the end of the 1950s, after the discovery of the gas fields at “Slochterveld”, we shifted our attention to natural gas. Petrogas was also involved in the first domestic connection to the Dutch natural gas grid.
employees
year of start
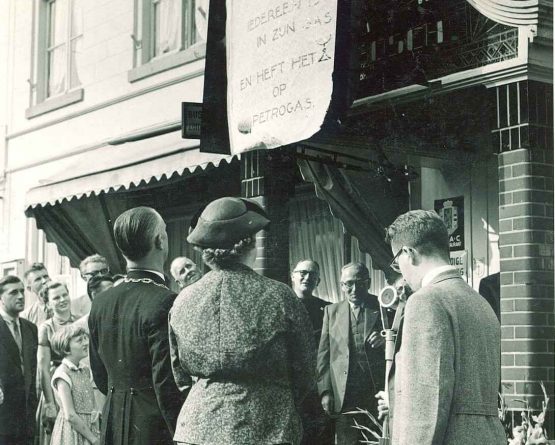
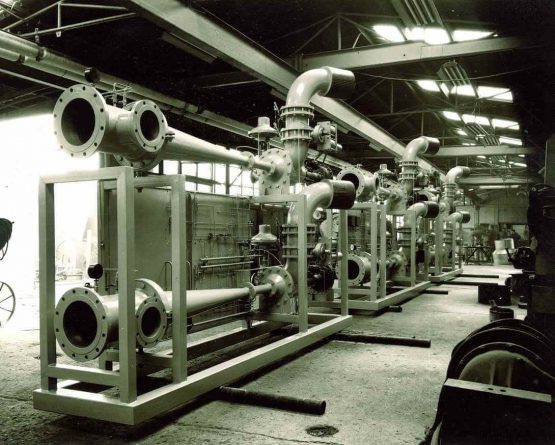
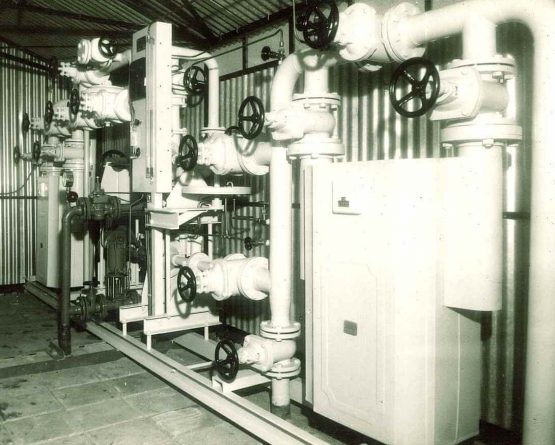
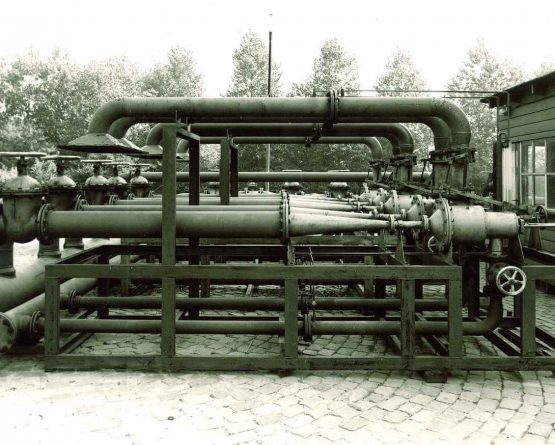
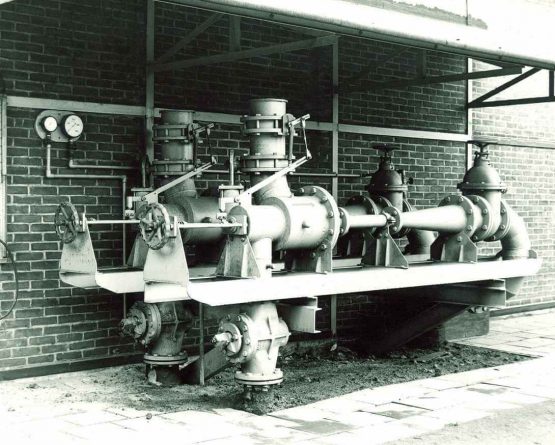
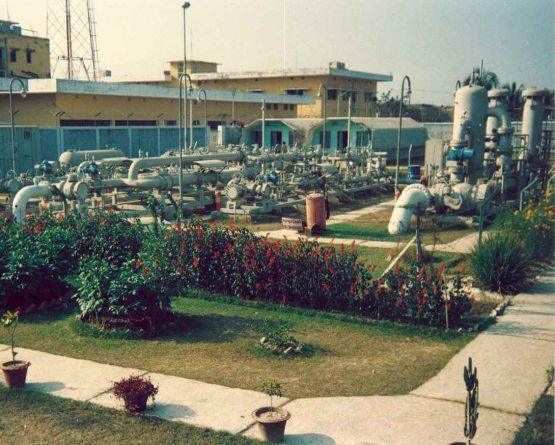
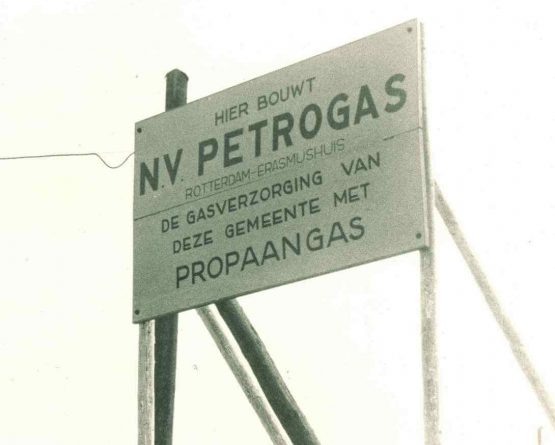
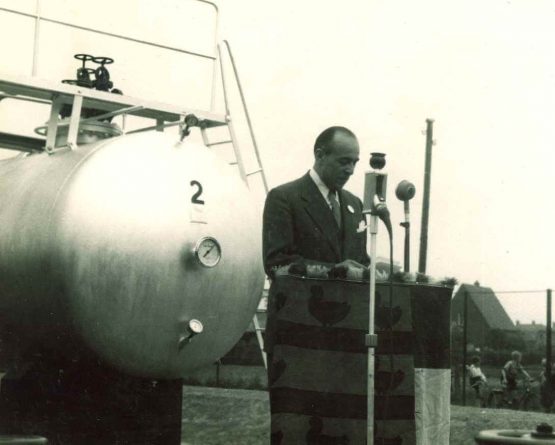
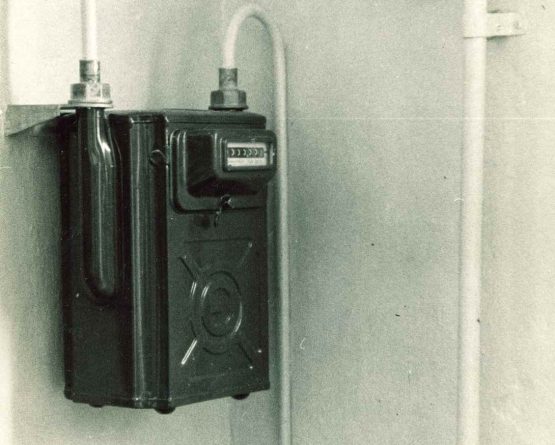
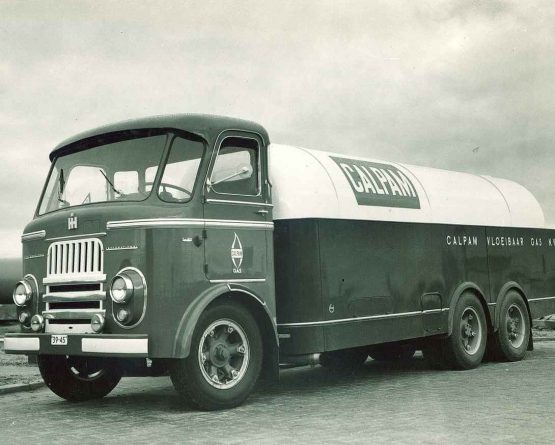
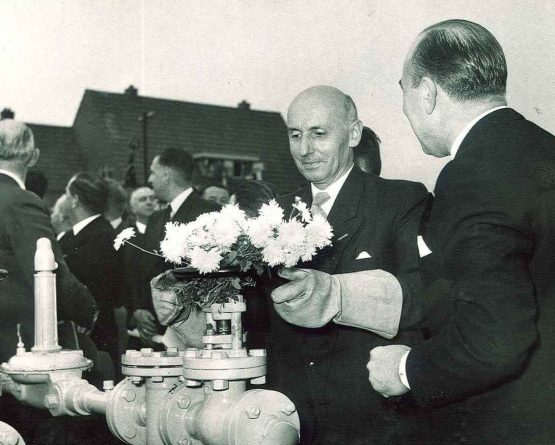
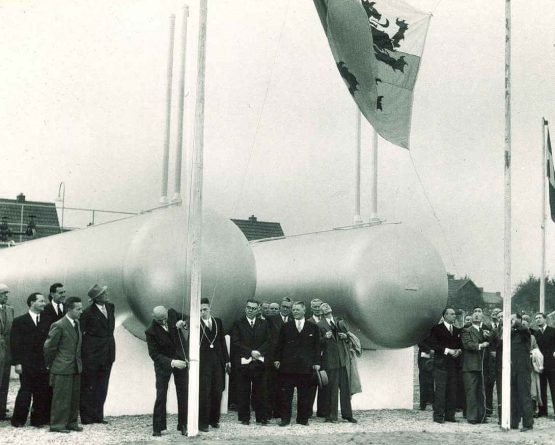
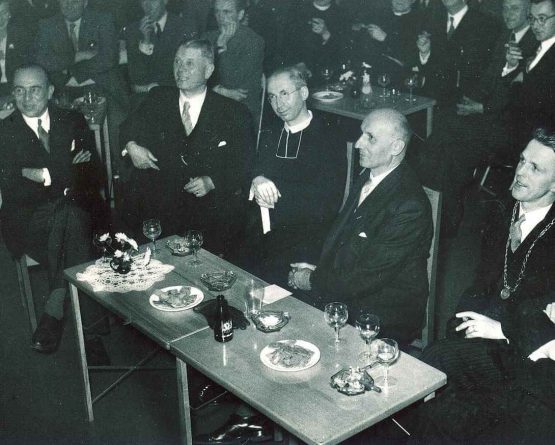
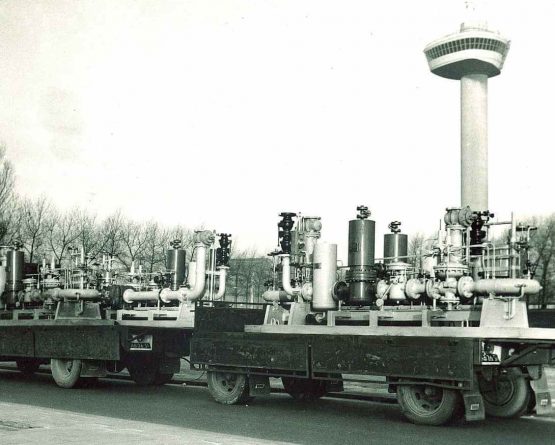
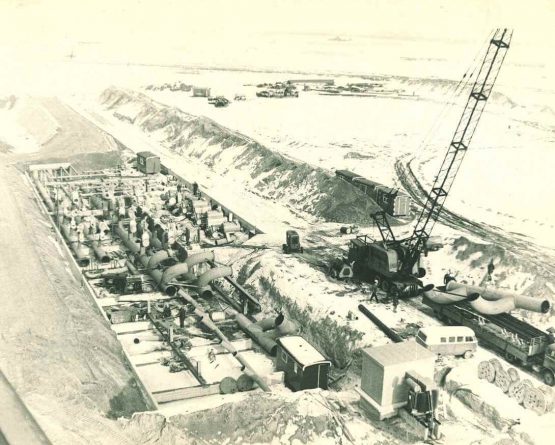
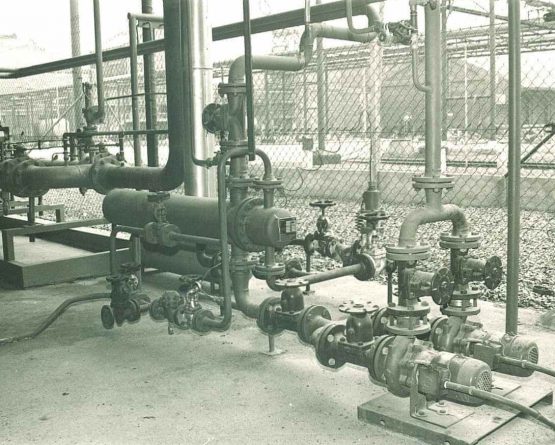
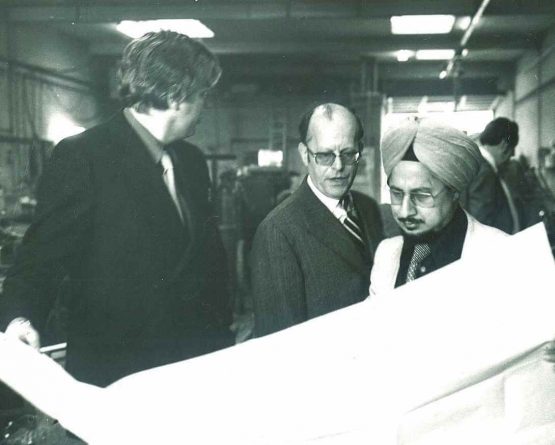
EXPANSION
Innovation and market expansion are core elements of our operational management.
Over the years, Petrogas has developed a stronger focus on energy production, in which sustainability plays an important role. By anticipating our customers’ needs and treating our customers as we would want to be treated ourselves, we have enjoyed significant growth.
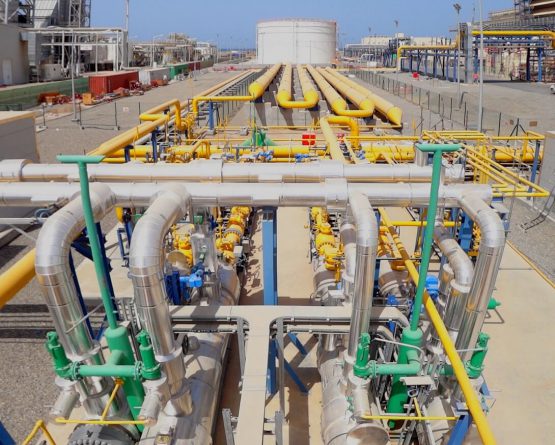
NOWADAYS
Our particular knowledge, skills and added value have helped us to build a solid reputation in a competitive market over the past 70 years.
We’re big enough to handle large and complex projects, but flexible enough to adapt quickly to changing circumstances. To do what we do, we must stay at the forefront of technology. Petrogas invests heavily in R&D, with the long-term focus of our innovation squarely on renewable energy production.
years of experience
countries with Petrogas representation
employees
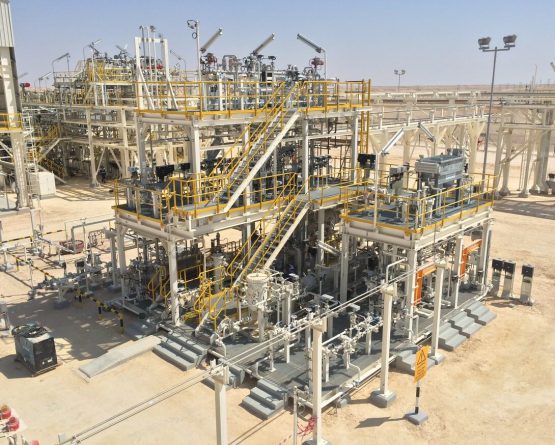
PRODUCTION FACILITIES
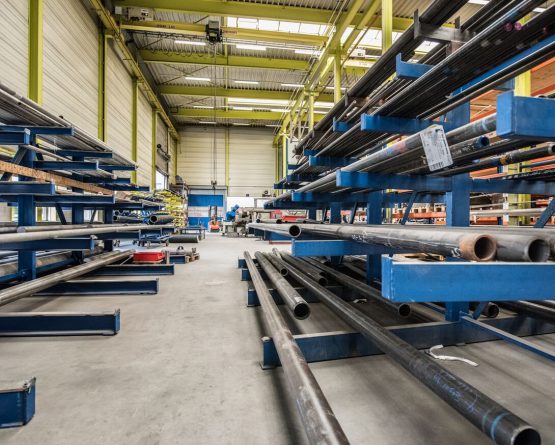
Warehouse
During this process materials are received and inspected according code and custom specific requirements. Materials are labelled and stored in a secured area. Quality controls on material certificates and heat numbers are in place and documented as required. Parts placement helps our operations to start jobs faster and in a controlled manner when planning determines to start. We believe in building in Quality at Source.
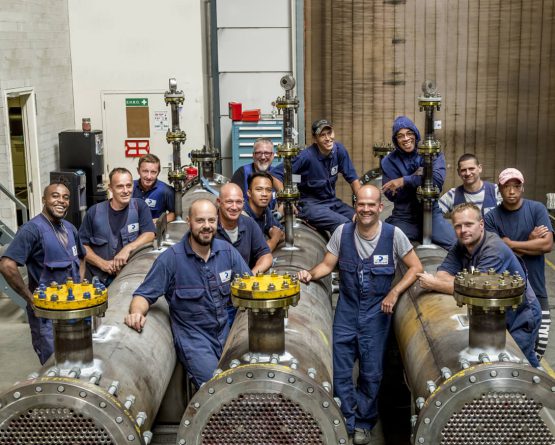
Welding
During this process raw materials are transformed into several components for your installation. Pressure vessels, Water bath heathers, heat exchangers and many others passing the hands of our welders. Trained skilled welders are working on several different types of welds – each with different types of materials and different variables such as temperatures and welding wires. Requirements regarding welding procedures are prescribed by the Code and can be extended by project specific requirements. Petrogas holds ASME U and R stamp and the welding quality ISO 3834-2 certificates. Besides visual inspection that includes X-rays and hydro testing up to 450 bar, ultrasonic, PMI (Positive Material Identification) and magnetic tests as required can be performed.
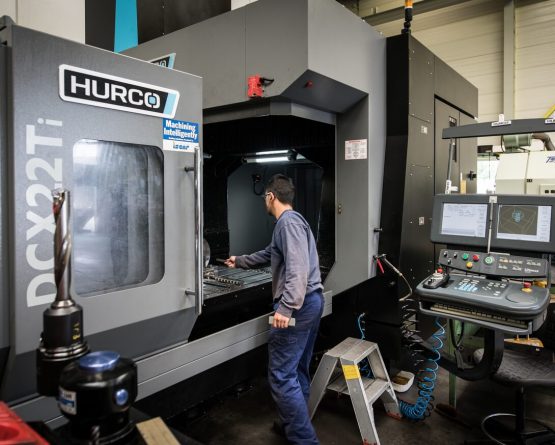
Machining
Our turning and milling machines produce all the custom engineered parts we need, from filter components right up to pressure vessels. Having our own machine shop gives us total control over quality, and keeps our costs and lead times to a minimum. It means we can be flexible – if a rush job comes in, we can quickly change priorities to handle it. A progress board helps us eliminate defects, continually improve health and safety issues and implement lean manufacturing. The planning board shows everyone which jobs are coming through on which machines, and the priorities. Everyone can see where each job is and where it’s going next. This level of transparency ensures there are no surprises in our workflow processes
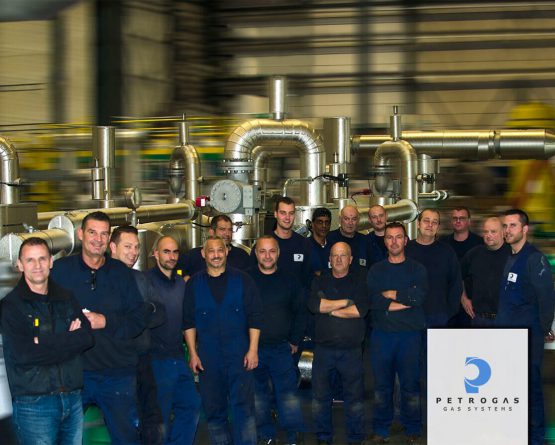
Assembly
During this process the manufactured components, skids, frames are received in their final coating and assembled by our trained assemblers. We have 15 people in the assembly department, working two shifts putting together the individual system sections themselves (inlet, filter, condenser etc.). Electrical assemblers connect up the wiring to the junction boxes and instruments, and the data telemetry that will go to the customer’s control room. All the system equipment is skid-mounted – along with process piping, instrumentation and safety equipment. We assemble everything before it leaves the factory to be sure that the equipment fits together properly. Quality conducts a final acceptance test and releases the installation for packing.
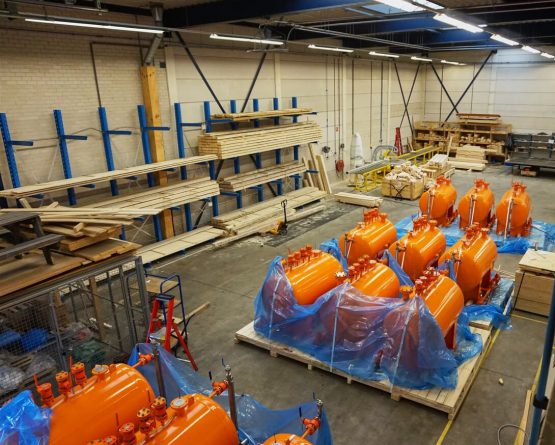
Packing & Transportion
Making sure your installation will be at your side in good condition that is the objective of our packing department. It does not matter how big the installation is , big or small we pack them all. Wooden packaging material meets the requirement of the ISPM 15 “Guidelines for regulating wood packaging material in international trade.” Together with the transport department all documents are prepared and inspections and labeling is in line according international and customer requirements.
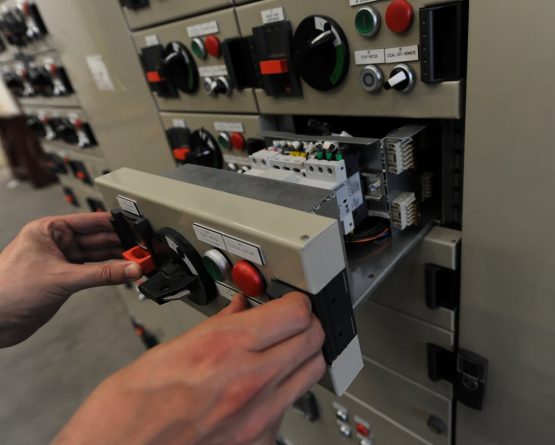
Control Panel Assembly
An separate department looks after the design and manufacturing of the control panel. An installation can be controlled with a control panel. This panel can be operated locally, but remote control from another site is also possible. The barriers, flow-computers, PLC’s and other computers are built into the control panels. Petrogas can deliver a special container in which the panel can be installed. The container can be supplied with facilities like air-conditioning, UPS and fire fighting equipment. Dimensions may vary according to customer’s specification.
Company Certificates
Every one of our installations is designed to our customers’ unique requirements , with quality and safety of course taking highest importance. We build quality into every process and production step from the start, particularly critical steps like incoming materials checking and welding. We believe in building in Quality at Source.
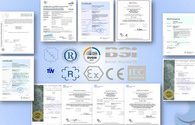
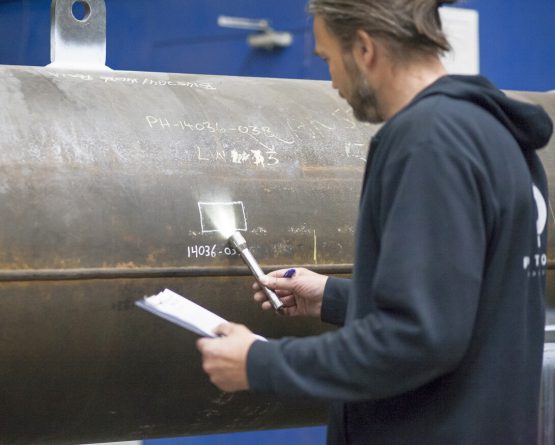
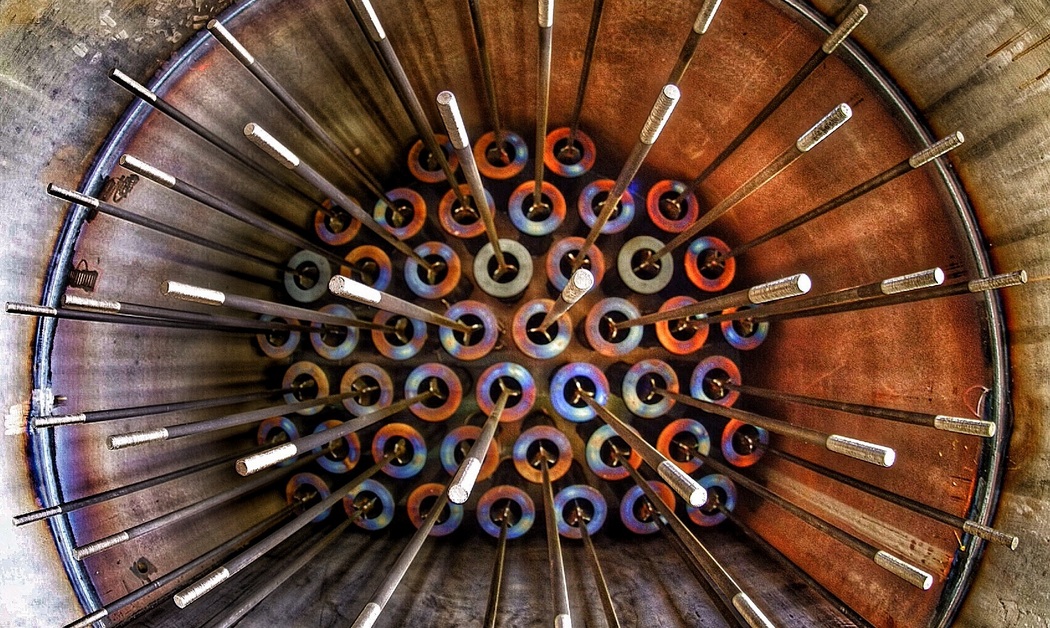
Filter Separator - Filter Cartridge Rack
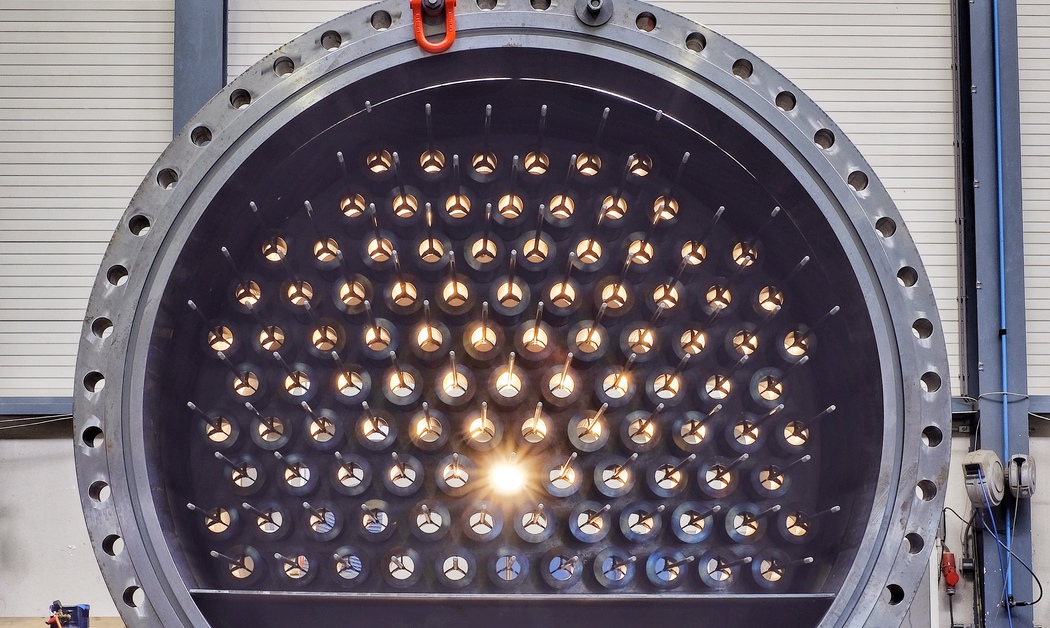
Filter Separator - Filter Cartridge Rack
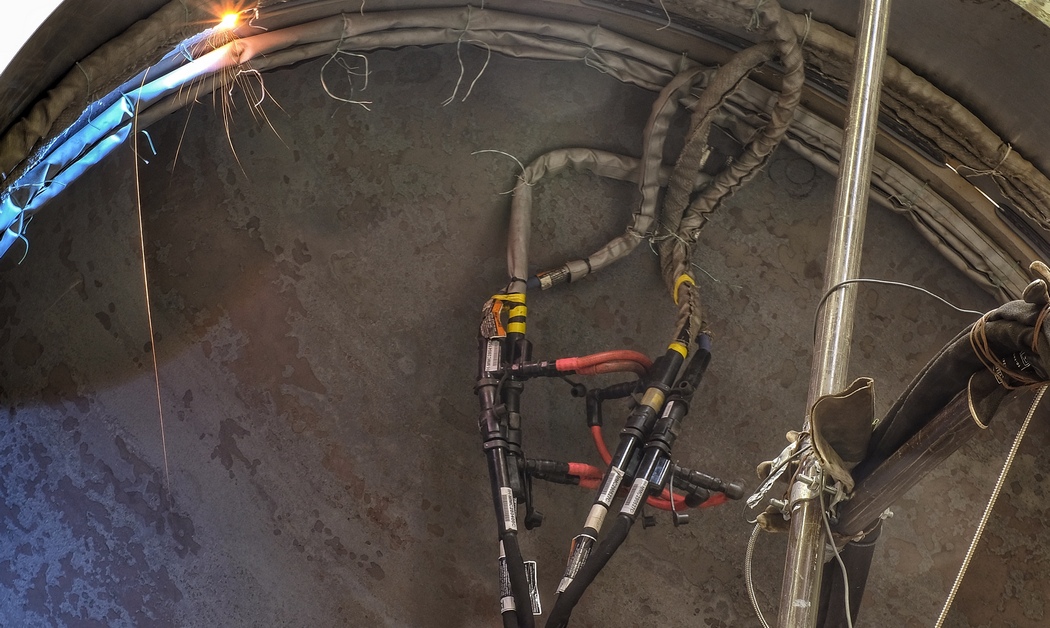
Submerged Arc Welding
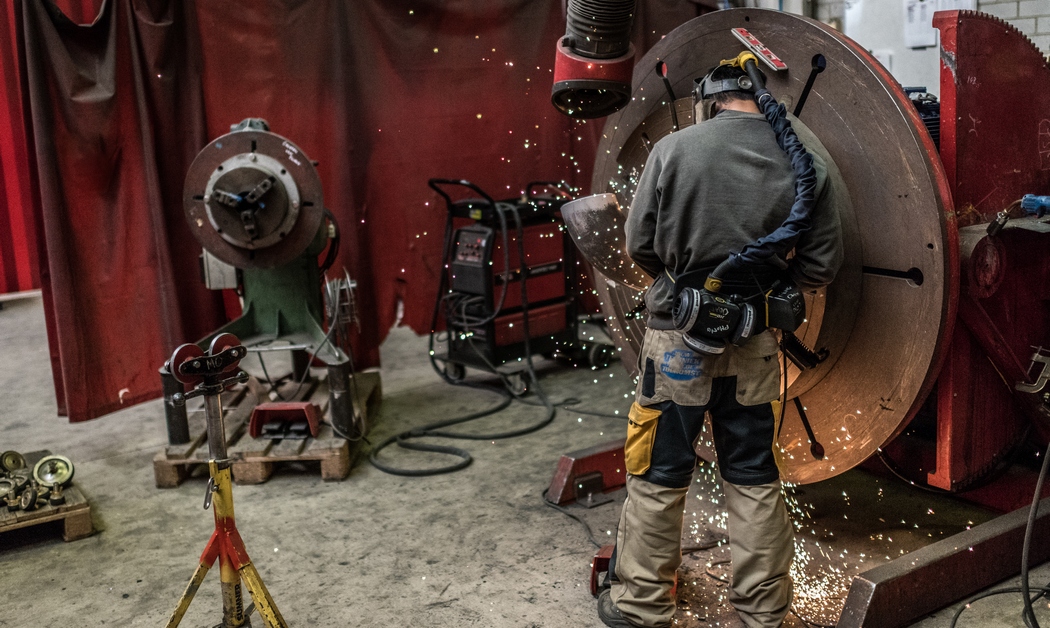
Welding Preparations
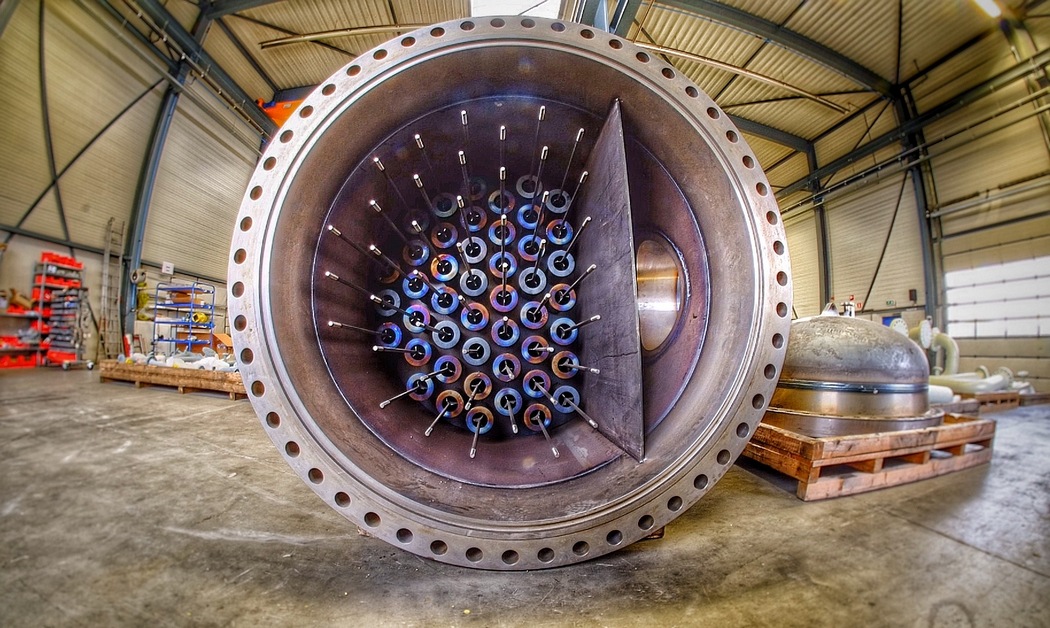
Filter Separator - Vessel Internals
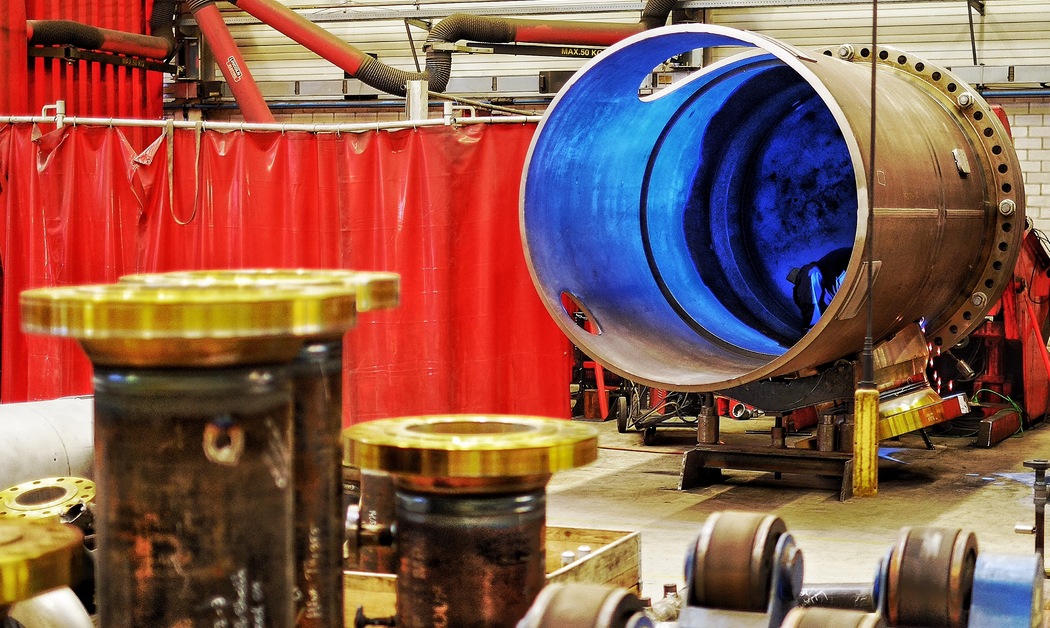
Welding
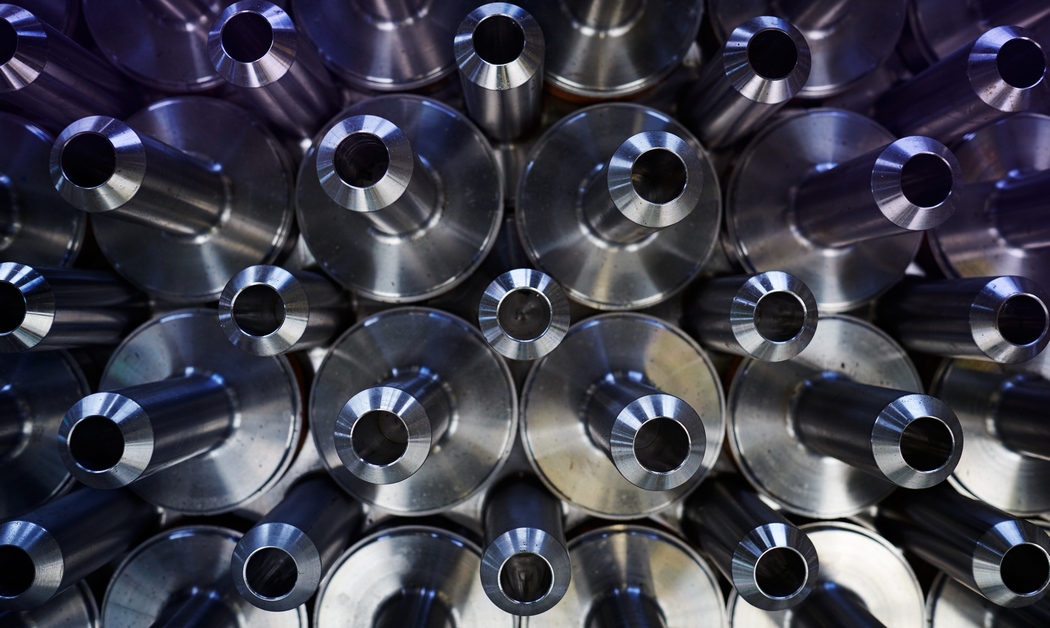
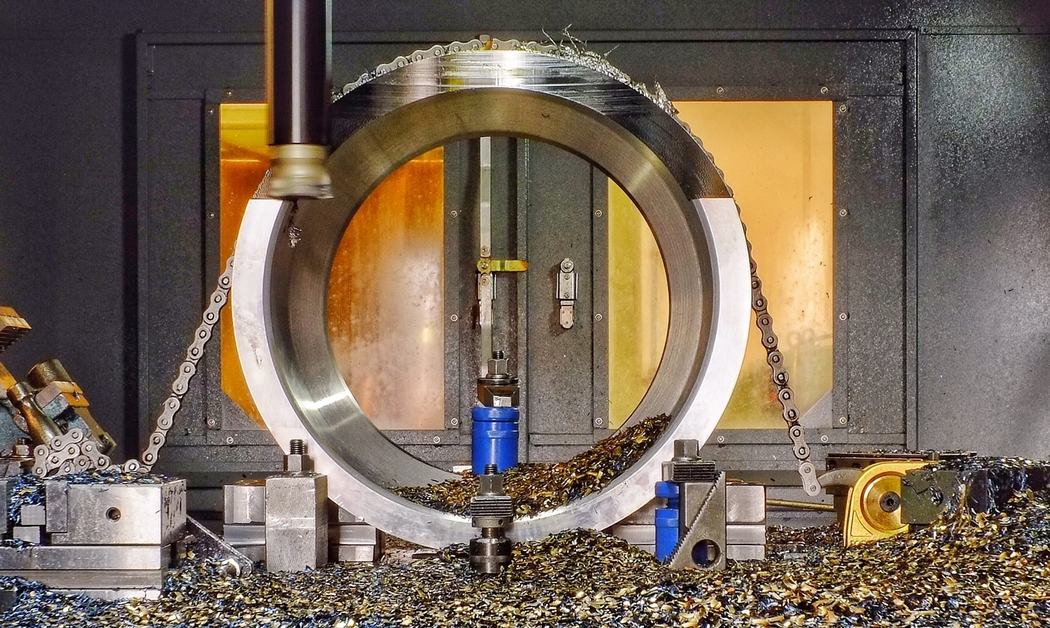
Milling
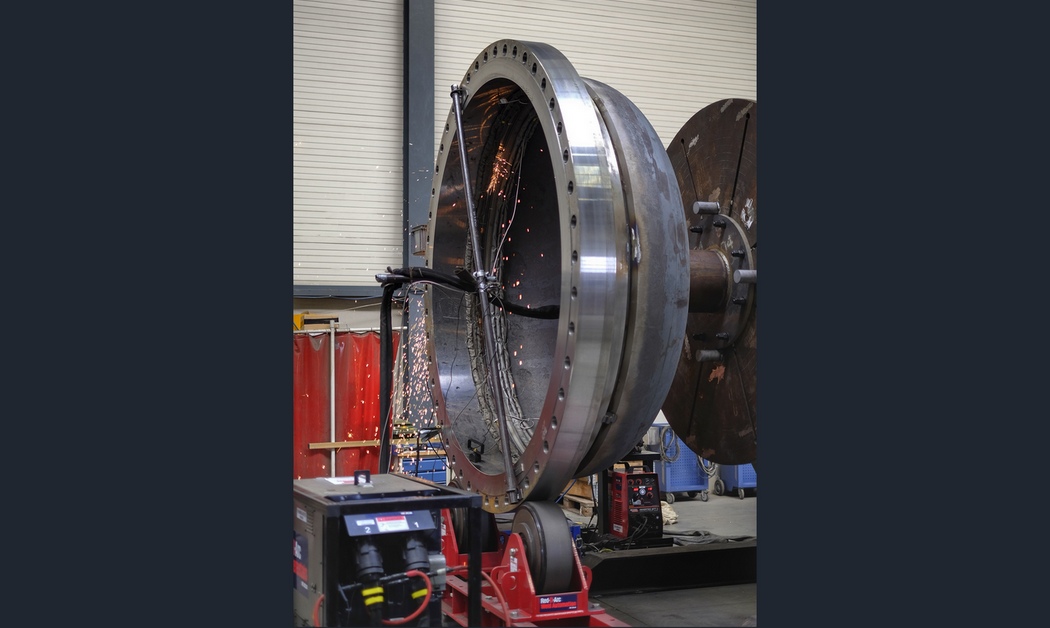
Submerged Arc Welding Preparations
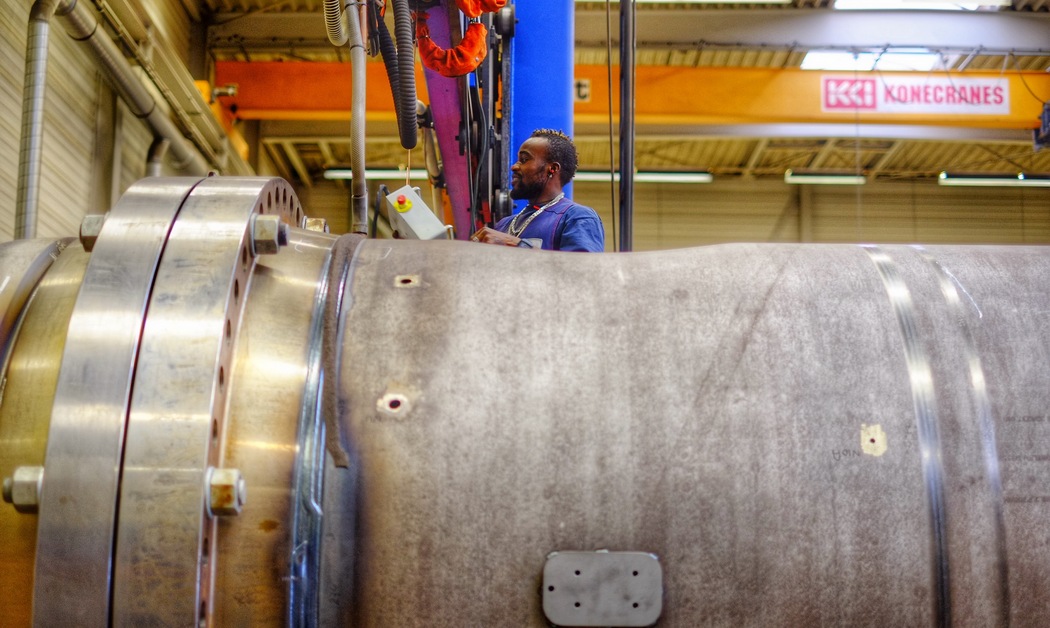
Submerged Arc Welding
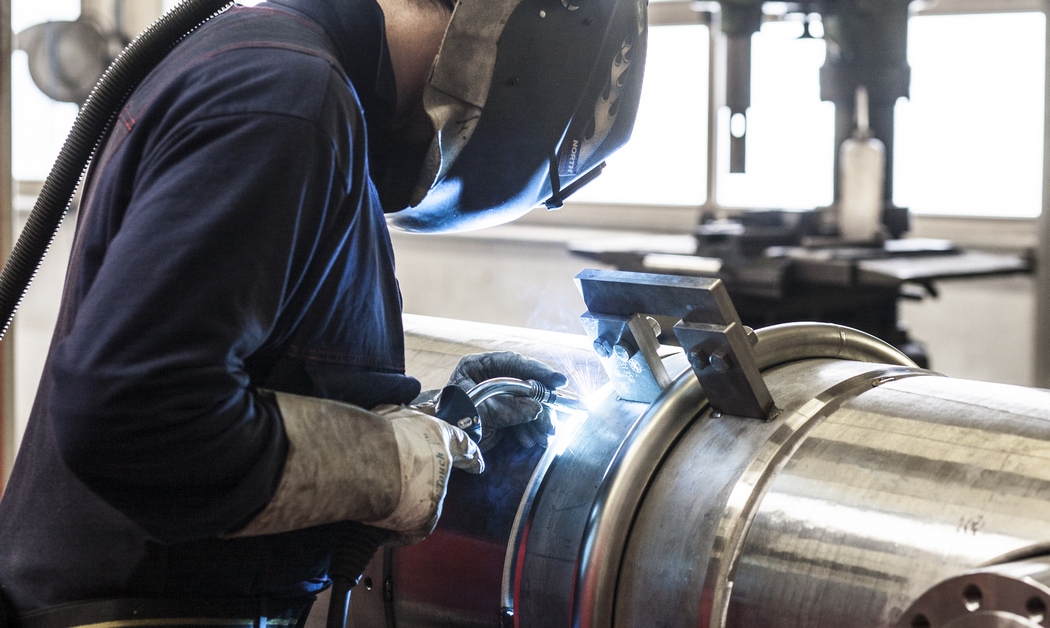
Stainless Steel Welding
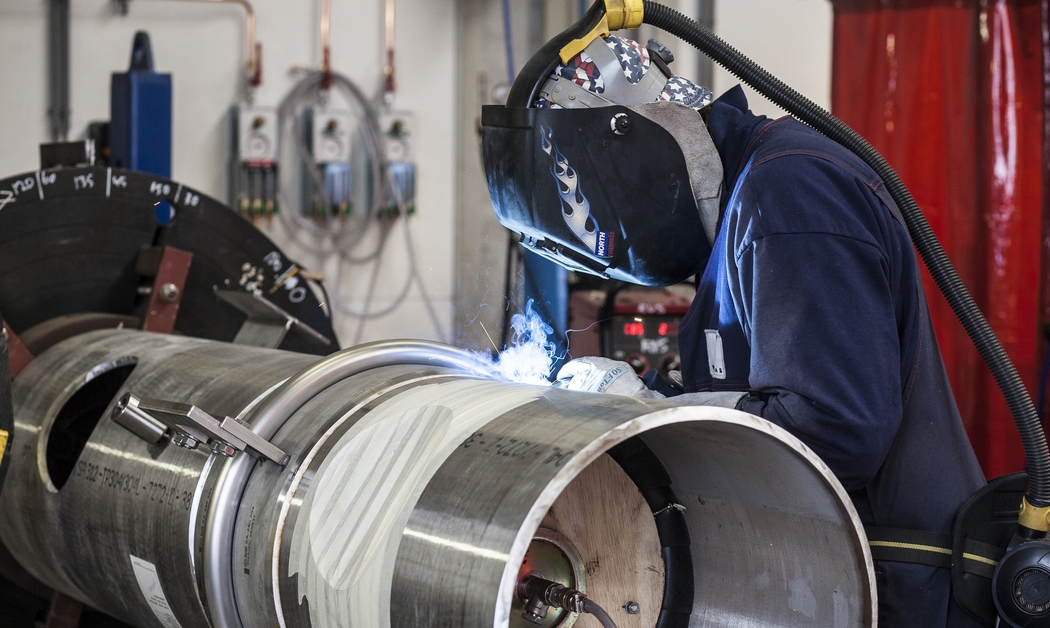